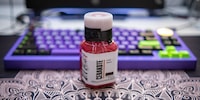
Background information
Keycap Kevin: my Cerakote adventure begins
by Kevin Hofer
I’m tarting up one of my keyboard cases with a ceramic coating – or at least trying to. My first time isn’t exactly going the way I’d like.
Can I make Cerakote myself? I keep asking myself the same question when looking at Reddit posts about keyboards with the ceramic coating. At some point, I decide to give it a try. I get everything I need – at least I think I do. Because as my journal shows, some things were forgotten and even more things went wrong.
I load the family car with my equipment. The Cerakote starter kit, sandblasting equipment, masking material and an oven. I thought Cerakote doesn’t need much. Turns out I was wrong. My boot reminds me of many family holidays.
After dropping my youngest off at daycare and running a few final errands, I arrive at my father’s house. I decided to work in his garage where I’m protected from the weather while simultaneously benefitting from great ventilation thanks to the open gate.
First, I soak my keyboard in acetone for half an hour. For my first attempt, I only worked on the keyboard top. I place it in a large metal casserole dish and add the acetone. The precious item must now stay in its bath for half an hour. This should dissolve any fat. In the meantime, I set up the rest of my equipment. Next up: sandblasting.
The air hose on my father’s compressor is too thin. For sandblasting, the inner diameter of your hose should be at least 10 millimetres in order to provide sufficient air. I need to go home and get a hose of my own. It won’t be the only time I lose time because I need to get something.
With a thicker hose, I can finally get started. Well, almost. The keyboard part still has to air dry first, which fortunately doesn’t take long with aluminium.
Now things can really get going. After all, I’ve only been at it for over two hours. Since my sandblasting gun has its container attached, I can’t really move it well in my homemade sandblasting booth. The gun plus the container are too big for my booth. Even worse, it’s too small for my keyboard part. And I’m not good at twisting and turning it.
But that’s not all: the blasting material in my gun’s container is used up so quickly that I have to refill it after less than a minute of blasting. Since I want to reuse the material, I sweep it up with a broom and shovel each time and return it to the container.
The work is very tedious and drags on. I blast for over an hour. At some point I can hardly see my device any more because of all the sand. In addition, my father’s compressor doesn’t have the necessary air volume. In other words, it lacks punch, dragging out the process even more. At one point, the 30-year-old compressor even gives up the ghost.
After buying my father a new compressor that delivers more air, things go faster. I really wanted to have the thing in the oven to cure before noon, but I’m just finishing sandblasting now. My verdict on sandblasting: be prepared – better than me.
After a short lunch break, the tour continues. I now need to prepare my device for painting. I attach two wires to the keyboard case to hang it later. Since Cerakote applies very thin layers, I don’t have to cover the wires. Before I can start spraying, I first put my workpiece in the oven and «bake» it for an hour at around 150 degrees. This should evaporate any residual liquid and grease.
I’m slowly running out of time. I have to leave in just over an hour to pick up the little one from daycare. Since I’m still frustrated from working all morning, I grant myself a break. I’m just now starting to get everything ready for spraying. In the process, I notice my spray gun requires quick couplings with a female thread. However, all my quick couplings for the compressor have a male thread. I need to buy one.
Since this eats up more time, I decide to call it a day. I’m afraid that I’ll make mistakes under time pressure. I’d rather get the coupling done in peace and prepare for spraying, which I plan to do the next morning.
We’re heading into the next round. All I need to do today is spray and cure my keyboard in the oven. I watched Cerakote’s official guide the day before and set up my spray gun accordingly. I first test the spray pattern on a piece of cardboard. It looks like I’m spraying a little too much colour at once, so I move the corresponding slider back a bit.
Now I can finally get to work. According to the instructions, I should spray the difficult areas first. There are quite a few on my piece. The corners at the cutouts for the F, navigation and arrow keys are especially difficult for a newbie like me. As I find out later, it’s where I fail the hardest.
After spraying, it’s time to cure. Finally, my keyboard is hanging in the oven. It must now remain there for two hours at around 120 degrees Celsius.
The two hours are up and my piece has cooled down enough. I can finally look at my work in detail. I like the colour I chose – Tungsten, similar to a shade I’d call anthracite. But that’s about it for the positives. Overall, I probably still sprayed too much paint. There’s lumps of paint in some corners, and I think there’s too much paint applied in general. I’ll need to try again. A day and a half of work down the drain.
Even though my first steps with Cerakote were mainly characterised by frustration, I want to keep at it. I think the process is too fun to give up. For now, I need some distance – and a proper sandblasting booth. In fact, sandblasting has had the most negative impact on my experience. Improving its efficiency should give me more energy and focus when spraying. I’ll keep you posted.
From big data to big brother, Cyborgs to Sci-Fi. All aspects of technology and society fascinate me.